Just how to Determine What is Porosity in Welding and Improve Your Technique
Unwinding the Enigma of Porosity in Welding: Tips for Reducing Issues and Making Best Use Of Quality
In the complex globe of welding, porosity continues to be a relentless challenge that can significantly impact the top quality and stability of welded joints. As we dig into the depths of porosity in welding, discovering the tricks to its prevention and control will be paramount for professionals seeking to understand the art of high-quality weldments.
Understanding Porosity in Welding
Porosity in welding, a common issue encountered by welders, describes the presence of gas pockets or voids in the welded product, which can endanger the honesty and top quality of the weld. These gas pockets are commonly entraped during the welding process as a result of numerous elements such as improper protecting gas, polluted base products, or incorrect welding criteria. The formation of porosity can weaken the weld, making it at risk to cracking and deterioration, inevitably causing structural failures.
By recognizing the significance of preserving correct gas shielding, making sure the tidiness of base materials, and maximizing welding settings, welders can considerably minimize the likelihood of porosity formation. Generally, an extensive understanding of porosity in welding is vital for welders to generate premium and sturdy welds.
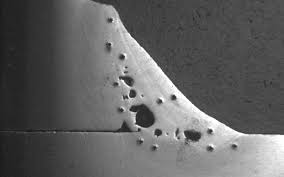
Usual Reasons of Porosity
When examining welding processes for possible high quality concerns, understanding the common root causes of porosity is essential for keeping weld honesty and avoiding architectural failures. Porosity, characterized by the existence of cavities or gaps in the weld steel, can substantially jeopardize the mechanical residential properties of a welded joint. One typical reason of porosity is incorrect shielding gas protection. Inadequate protecting gas circulation rates or incorrect gas combinations can result in climatic contamination, leading to porosity formation.
Furthermore, welding at inappropriate specifications, such as excessively high traveling rates or currents, can create too much disturbance in the weld swimming pool, trapping gases and causing porosity. By dealing with these usual reasons via appropriate gas protecting, material preparation, and adherence to ideal welding specifications, welders can minimize porosity and boost the quality of their welds.
Methods for Porosity Prevention
Executing efficient preventive procedures is vital in lessening the event of porosity in welding procedures. One technique for porosity prevention is making sure appropriate cleansing of the base metal prior to welding. Contaminants such as oil, oil, corrosion, and paint can lead to porosity, so extensive click cleaning making use of proper solvents or mechanical techniques is necessary.

Using high-grade filler products and shielding gases that are suitable for the base metal and welding process can significantly reduce the threat of porosity. Furthermore, keeping correct welding specifications, such as voltage, existing, take a trip rate, and gas circulation rate, is vital for porosity prevention.
Furthermore, using correct welding strategies, such as preserving a consistent travel rate, electrode angle, and arc length, can aid protect against porosity (What is Porosity). Ample training of welders to guarantee they comply with best techniques and high quality control treatments is also necessary in lessening porosity problems in welding
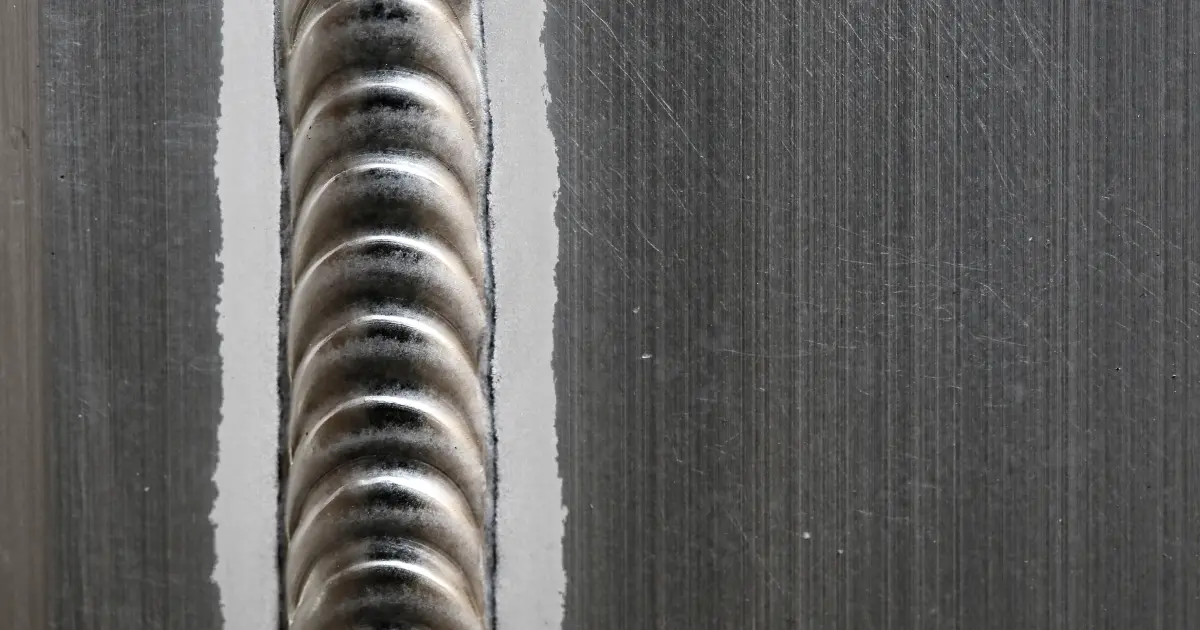
Ideal Practices for Top Quality Welds
One key practice is keeping appropriate sanitation in the welding area. Extensively cleaning up the workpiece and surrounding location before welding can assist mitigate these issues.
One more finest practice is to very carefully choose the appropriate welding criteria for the specific products being signed up with. Proper parameter selection makes sure optimal weld infiltration, combination, and general top quality. Making use of high-quality welding consumables, such as electrodes and filler metals, can dramatically impact the final weld high quality.
Relevance of Porosity Control
Porosity control plays a vital role in making certain the stability and quality of welding joints. Porosity, characterized by the presence of cavities or spaces within the weld steel, can significantly compromise the mechanical residential or commercial properties and structural stability of the weld. Too much porosity deteriorates the weld, making it extra at risk to splitting, rust, and general failing under operational tons.
Effective porosity control is crucial for preserving the desired mechanical homes, such as strength, ductility, and strength, of the bonded joint. What is Porosity. By reducing her comment is here porosity, welders can improve the overall high quality and integrity of the weld, ensuring that it fulfills the efficiency requirements of the intended application
Moreover, porosity control is essential for achieving the desired visual look of the weld. Extreme porosity not just damages the weld yet likewise takes away from its visual allure, which can be crucial in sectors where aesthetic appeals are very important. Appropriate porosity control strategies, such as utilizing the proper protecting gas, regulating the welding specifications, and making certain proper tidiness of the Read Full Article base materials, are essential for generating high-quality welds with very little problems.
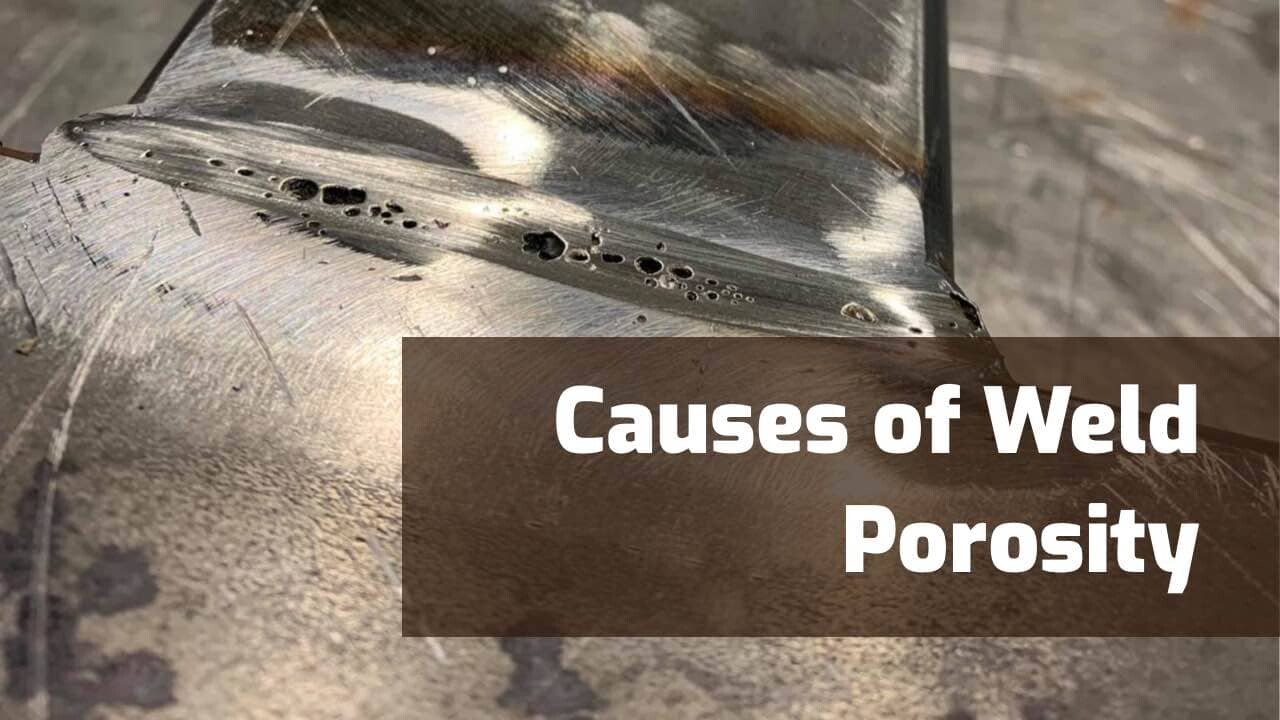
Conclusion
In conclusion, porosity in welding is an usual defect that can jeopardize the high quality of the weld. By comprehending the reasons for porosity and applying appropriate prevention methods, welders can minimize flaws and accomplish greater top quality welds. It is vital to regulate porosity in welding to ensure the stability and stamina of the end product. Implementing ideal practices for porosity control is vital for attaining optimum welding results.